MGD and PSC Mindsets: Bridging the Understanding Gap
- Feb 4, 2021
- 0 Comments
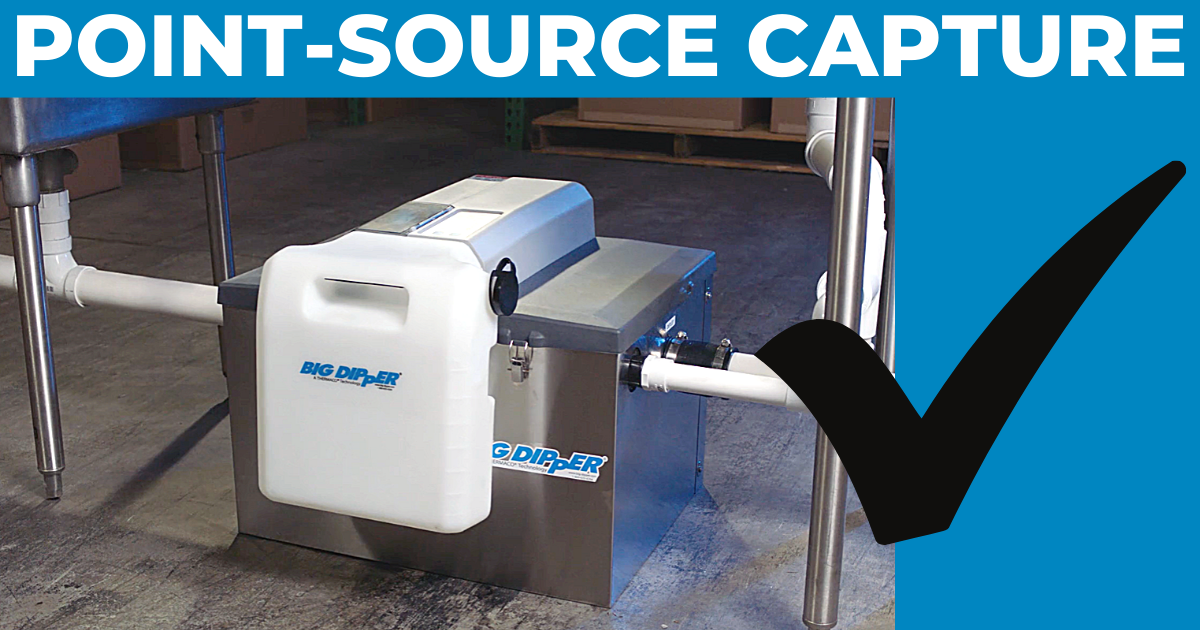
We speak to anyone with a FOG (fats, oils and grease) inquiry and often end up pointing them in a totally different direction than they originally were headed. It’s a pattern in these conversations. Occasionally, this involves a caller with an MGD (million gallons per day) mindset. Here is an example of how one of these calls typically proceeds.
Caller: I have a grease problem and am trying to figure out which of your products to specify.
Bill: Tell me about your problem.
Caller: We have an on-site wastewater treatment plant and are having operational issues.
Bill: Ok, you have an on-site WWTP. Tell me more about your issues.
Caller: We have Nocardia filamentous bacteria raging in our plant because of high influent grease loading. This stuff is not forming floc. It’s sludge bulking our clarifier and causing out-of-limits turbidity in the final effluent.
Bill: Ok, I understand your situation. What’s feeding into your plant?
Caller: We get an average of 0.25 MGD into our plant from a 600-room resort hotel together with flows from 96 condominiums.
Bill: A resort complex, yes? Tell me about the restaurants and bars at this resort.
Caller: There is a four-star steakhouse, a 24-hour diner, a beach grill, and a catering kitchen that can feed as many as 1,500 meals in one sitting for large conferences and/or multiple weddings or parties.
Caller: So what size grease separation unit do I specify at the headworks?
Bill: You want to put a grease separator at the headworks?
Caller: Yes. Please tell me the installation footprint and its electrical requirements.
Bill: Ok, I understand what you would like to have. Unfortunately, there is nothing I am aware of that can be installed at the headworks to remove the FOG from the influent stream.
Caller: What?
Bill: Trying to get grease/oils out of a 0.25 MGD stream using gravity separation is impossible.
Caller: How are we going to reduce the high FOG load coming into our plant?
Bill: To control the Nocardia, you want to drastically reduce the FOG in the influent to your wastewater treatment plant, yes?
Caller: Yes, absolutely!
Bill: Ok, are there upstream grease separators servicing the steakhouse, the 24-hour diner, the beach grill and the bars?
Caller: We have a 5,000-gallon grease separator receiving the steakhouse’s flows, the 24-hour diner and the bar inside the hotel. The beach grill and bar have a 1,000-gallon grease separator. A pumping company pumps out those separators once a month.
Bill: When you look into the separators, what do you see?
Caller: All I see is milky, gray water and a puddle here and there of floating grease.
Bill: Ok, this is good information. You have Nocardia at your treatment plant, causing clarifier bulking, high levels of turbidity and all the factors pointing to high grease input loads. Yet, the upstream grease separators are not showing floating grease mats as expected. This tells us the grease is getting chemically emulsified prior to the grease separator and likely continuing to be emulsified while in the grease separator.
Caller: Are you saying the grease separators are not working?
Bill: They work fine with free-floating fats and oils. Grease/oil/detergent emulsions are another story. Emulsions are essentially like milk or anti-freeze in your car radiator. Once they form -- the emulsion, that is -- it cannot be separated. All of the grease going down the kitchen drains is going to your treatment plant, where the bugs jump on the detergent first and release the grease and oils to feed the Nocardia. It does not help that the resort is located in a hot climate that makes Nocardia really happy.
Caller: This sounds hopeless. We have to operate the restaurants, we have to meet the local limits and we have to reduce our operating expenses. Do we change detergents? What can we do?
Bill: Yes, there are two steps that can be implemented to keep the grease and oils from reaching your treatment works.
Bill: First, put separators at every FOG entry point before the FOG gets mixed with wastewater flows from hotel rooms, conference area restrooms, and other parts of the resort. Second, educate the staff to follow Best Management Practices for reducing waste going into the drains.
Caller: We are a consulting engineering firm. We don’t have anything to do with the resort’s operations.
Bill: I understand. Again, there is nothing I am aware of that can be stationed at the WWTP headworks to remove FOG from the influent. You want it out, yes? The optimum path is to control and manage the point-sources. This has been done with success at many resorts with on-site treatment plants.
Caller: Ok, you are telling me it is not possible to do this at the headworks. Wow! This was not part of the original resort plan, and I don’t know if they will make those changes in the kitchens.
Note: The phone call sometimes ends at this point. The caller, usually a consulting civil engineer who is an expert in designing and operating on-site wastewater treatment operations, is disheartened because his/her MGD mindset has been rocked.
Bill: The influent grease problem can be solved and, yes, it involves getting the resort’s management on-board with installing upstream equipment and instituting best management practices in the kitchens.
Caller: Are you sure installing separators at or near the point sources will do the job? This is a big ask for these folks. They hired us to solve the problem. Now I’m learning the problem to be solved is not at the WWTP. It’s inside the kitchens.
Bill: We can give you references to folks who went down this same path. Basically, if the grease and oils are captured as soon as they enter the drainage system and before mixing with subsequent flows, your treatment plant does not receive FOG in the effluent. Additionally, there are some source points requiring separate management to ensure minimum FOG loading arrives at your headworks.
Caller: Such as?
Bill: The pre-rinse sinks ahead of the dishwashers. It is important to capture the grease from those points BEFORE it mixes with the hot, soapy water from the adjacent dishwasher.
Caller: What makes those pre-rinse sinks special?
Bill: Those sinks get the plates from the dining rooms and conference room meals. The plates have salad dressing, butter, residual oils, and other fats. Standard commercial dishwasher practice is to rinse those plates before racking and washing them in the dishwasher. So, you can see they are heavy FOG loading entry points at the resort. If that grease is allowed to mix with the hot, soapy dishwasher effluent, it gets chemically emulsified. There is no gravity separator on earth capable of separating a detergent-oil/fat emulsion. Yes, it is critical to capture the fats/oils immediately at the pre-rinse sink.
Caller: Wow, I am overwhelmed. (This is typical for an MGD mindset being confronted with a logical path forward involving PSC [Point Source Capture] thinking.) I am going to run this up the flagpole to see how resort management views this solution.
Bill: We understand. At first, they will not like it because it involves changes in their kitchens. If the goal is to eliminate the filamentous bacteria problem at the WWTP, this is a bolt-on fix. Good luck! Let us know how we can be of further service.
Caller: Will do. Thanks.
Postscript:
The MGD mindset certainly has its place. No argument there. PSC also has its place. Our 36 years serving the foodservice industry and sewer district communities has taught us:
- Capture and removal of FOG, food and other organic loadings at point sources is the optimal solution set.
- Point-source capture can enable the downsizing of on-site treatment plants.
- Point-source capture creates a virtuous information feedback loop. When the downstream WWTP sees an increase in FOG, it triggers on-site inspections of the point-source separators and staff meetings (usually new staff unaware of previously implemented best management practices). This leads to less waste put into drains and better waste handling practices.
- Everyone understands their impact on the downstream WWTP. Awareness is a big part of an ongoing healthy water treatment management program.